Lessons from Past Workplace Accident Stories
Each year, billions of dollars are lost by businesses due to employee accidents in the workplace. When an accident occurs, the employer may be responsible for paying the injured employee’s medical bills.
Additionally, most workplace injury stories involve legal issues and procedures that can cost the employer thousands of dollars in legal bills. If the employee can no longer work due to the injuries sustained in the accident, the employer must absorb the costs of hiring and training a new employee.
Despite this, most workplace accidents are easily preventable. The Occupational Safety and Health Administration (OSHA) has extensive regulations that employers are required to follow to help prevent accidents and ensure employee safety.
Furthermore, employers often have their own safety policies and procedures designed to provide employees with a safe work environment. If employers and employees had followed the established rules, many accidents would never happen. By reviewing past accident stories in the workplace, it may be possible to avoid similar incidents in the future.
Construction Accident Stories: Thomas Patane
One early morning in May of 2014, 26-year-old Thomas Patane was part of a construction crew working on PS 313, a new elementary school being constructed in Queens, New York. A 911 call was made to the police reporting that someone had fallen down an elevator shaft.
For reasons that are unclear, Patane (who was working on the fifth floor) fell down the elevator shaft to the basement. He was rushed to Elmhurst Hospital Center, where he was pronounced dead. Though the accident is still being investigated, Patane was reportedly wearing a safety harness that was not attached to a lifeline as required by OSHA.
On the same day, at the same construction site, a second construction worker fell down the elevator shaft. This worker fell more than six feet from the second floor to the first floor. He was wearing a safety harness that was attached to a lifeline. This worker survived the fall with non-life-threatening injuries.
OSHA has very strict safety regulations designed to prevent construction workers from falling. Falls are the most common type of construction site accident. Most of the safety requirements are meant to be in place in when workers are working at elevations above six feet.
Fall protection measures (such as a personal fall arrest systems) are meant to prevent accidents such as Patane’s. Workers wearing safety vests that are attached to lifelines prevent workers who fall from dropping more than six feet.
Workplace Accident Stories: Randy J. Austin
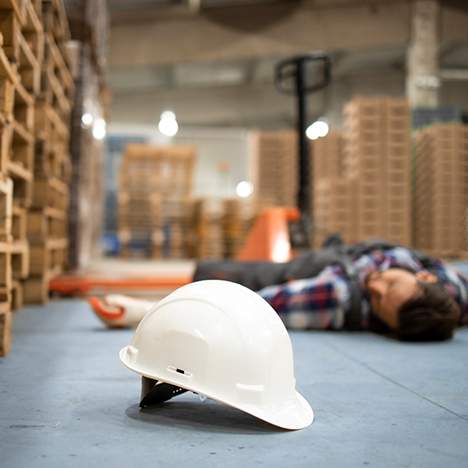
In July of 2009, Randy Austin, an employee of Kroger, was told to clean a slick spill in the restroom of one of the stores. Kroger had a policy that required employees to use a product called “Spill Magic” to clean spills. The use of Spill Magic reduces slip and fall accidents by 25%.
On the day that Austin had to clean the spills in the bathroom, the Spill Magic stations were not stocked. Instead of using Spill Magic, Austin used a dry mop and bucket to clean the spills. Despite being particularly careful, during the cleaning process Austin fell and suffered serious injuries to his femur and hip.
Kroger’s Safety Handbook required that management make sure that Spill Magic was available at all times at several places throughout the store. On the day of Austin’s accident, no Spill Magic was available. While there is no guarantee that if Spill Magic had been available he would not have fallen and suffered a serious injury, there is a chance that its use would have prevented the accident.
As a result of the accident, Austin is suing Kroger to recover damages related to the accident and his injuries. The case is still pending.
Consequences of Failing to Follow Safety Rules
In many cases, the employer will end up being responsible in workplace accidents stories. In most cases, workplace accidents are covered by workers’ compensation, and the injured employee or their family will receive benefits.
When the employer does not have workers’ compensation insurance, as in the case of Kroger, then the employee may be able to recover damages from the employer after filing a personal injury lawsuit.
Preventing Falls at Construction Sites
The above-referenced news release states that falls are a leading cause of death for construction workers. According to a Cal/OSHA Fact Sheet, the use of certain safety equipment can reduce or eliminate the risk of falls on construction sites:
- Personal fall arrest systems consist of a horizontal line secured to the back and to a harness above the worker’s waist. The lifeline system prevents workers from falling more than six feet. The point where the line is anchored must be able to support 5,000 pounds per worker, and the line itself must have a breaking strength of at least 5,000 pounds.
- Positioning devices are systems of ropes and body harnesses that leave the individual’s hands free to work. The anchorage point must be able to support 3,000 pounds, or two times the intended load, whichever is greater.
- Personal fall restraint systems are body belts or harnesses attached to a lifeline. The anchorage point base must be rigged to allow movement only to the edge of the work area, and must be able to support four times the intended load.
- Approved safety nets should be used on working heights of twenty-five feet or more when personal fall protection or other types of protection are not practical. Nets must be tested before use.
Construction Site Hazards
Construction sites have their own set of safety hazards (which include elevated areas, moving equipment, power lines, and open trenches), and they are particularly susceptible to workplace accidents, resulting in countless construction injury stories.
There are a number of different trades involved in the construction industry, each with its own set of hazards, which include plumbers, painters, electricians, insulation workers, drywall installers, carpenters, welders, heavy equipment operators, and hazardous waste workers.
Construction workers are exposed to primary hazards from their own jobs and bystander hazards from others who are working nearby.
The four basic types of construction industry hazards are:
- Chemical: including acids, lead, solvents, and asbestos
- Physical: including falls, machine dangers, noise, and electricity
- Biological: including bacteria, mold, and blood-borne pathogens
- Social: including dwindling construction orders, unstable employment, adverse weather conditions, and other economic or societal factors
Cal/OSHA’s stated goal is to raise awareness among those working in construction that hazards can be identified and corrected. Employers who do not comply with safety regulations will be issued citations and ordered to correct violations.
Workers’ Comp vs. Personal Injury Law: When to Hire a Lawyer
If you’ve been injured on the job, it’s important to know the difference between workers’ comp and personal injury cases, as well as when it’s necessary to hire a lawyer. Speaking with an attorney who is familiar with workplace injury stories and cases is the fastest way to find out if you are owed compensation for an incident you’ve been involved in.
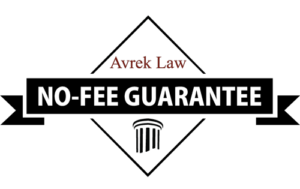
Not sure if you have a case? At Avrek Law, we offer free, no-obligation consultations. With over $2 Billion recovered in over 45,000 cases, we’re here to help – call us today!